Seals can prevent lubricants from escaping and stop dust, water and other harmful substances such as metal particles from getting into the bearing. By doing so, they help to ensure that bearings last as long as possible. Seals must not cause excessive friction and should only allow a small amount of seal wear. External seals should also be easy to fit and remove.
Certain of the bearings in NSK’s catalogue are pre-sealed. These include Molded-Oil bearings, for example, which are lubricated with NSK’s own oil-impregnated material, Molded-Oil, and used in corrosive and dusty environments.
It is important to choose the right seal for each application, taking the lubrication method into account.
NSK non-contact seals
Some types of seal do not come into contact with the shaft. These include oil groove seals, flingers and labyrinth seals, for example. As they have little running clearance, they usually have a sufficient sealing action. Centrifugal forces also help to prevent contaminant ingress and lubricant loss.
1. Gap seals
Gap seals feature a thin cavity between the shaft and the housing and have multiple grooves in the housing bore, the shaft surface or both.
If simple gap seals alone are not enough, a flinger or labyrinth seal is often combined with the gap seal (not suitable for low speeds).
The grooves are lubricated with a grease which has a worked penetration of approximately 200 to prevent dust from entering the bearing. The thinner the cavity between the shaft and the housing, the more effective the seal is. However, the shaft and the housing must not come into contact with one another during operation.
A width of approximately 3 to 5 mm and a depth of around 4 to 5 mm are recommended for the grooves. If the seal relies on grooves alone, it should have three or more grooves.
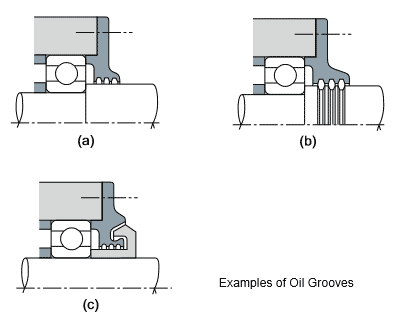
2. Seal with a flinger (oil slinger)
A flinger deflects water and dust with the aid of centrifugal forces. Seal mechanisms with labyrinth housings are primarily designed to prevent oil leaks and are mainly used in relatively dust-free environments.
3. Labyrinth seals
Labyrinth seals are made up of interlocking segments on the shaft and housing which are separated by a very small gap. They are particularly well suited to preventing oil leaks around the shaft at high speeds.
NSK contact seals
Contact seals work by means of physical contact between the shaft and the seal. They can be made from materials such as synthetic rubber, synthetic resin or felt. Radial shaft seals with rubber lips are the most common type.
1. Radial shaft seals
Many kinds of radial shaft seals are used to prevent lubricant leaks and to stop dust, water and other foreign bodies from entering the bearing.
As a lot of radial shaft seals have garter springs to generate the necessary compression force, oil seals are also suitable for shafts with irregular rotation to some extent.
The sealing lips are usually made from synthetic rubber containing nitrile, acrylate, silicone or fluorine. Tetrafluoroethylene is also used. The materials are listed in order of their maximum permissible operating temperature, with the highest last.
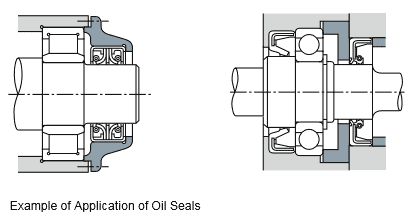
Radial shaft seals made from synthetic rubber can lead to problems such as overheating, wear and seizing if there is no oil film between the sealing lip and the shaft. For this reason, a small amount of lubricant should be applied to the sealing lips when the seals are installed. Ideally, the seal sliding surface should also be coated with lubricant regularly from the inside. The permissible peripheral speed for radial shaft seals varies depending on the type of finish on the shaft’s surface.
The temperature range for radial shaft seals is restricted by the material used for the sealing lips. If radial shaft seals are used at high peripheral speeds or exposed to high internal pressure, the shaft’s contact surface must be smoothly finished and the concentricity should be less than 0.02 to 0.05 mm. The shaft’s contact surface should be hardened by means of heat treatment or hard chrome plating in excess of HRC 40 to increase abrasion resistance. A hardness of over HRC 55 is recommended wherever possible.
Seal Materials | Permissible Circumferential Speeds (m/sec) | Operating Temperature Range (°C) | |
---|---|---|---|
Synthetic Rubber | Nitrile Rubber | Under 16 | –25 to +100 |
Acrylic Rubber | Under 25 | –15 to +130 | |
Silicone Rubber | Under 32 | –70 to +200 | |
Fluorine-containes Rubber | Under 32 | –30 to +200 | |
Tetrafluoride Ethylene Resin | Under 15 | –50 to +220 |
Circumferential Surface Speeds (m/s) | Surface Finish Ra (µm) |
---|---|
Under 5 | 0.8 |
5 to 10 | 0.4 |
Over 10 | 0.2 |
1. Felt seals
Felt seals are among the simplest and most common seals. They are used for applications such as gear shafts. If oil is used as a lubricant, it can soften the felt, which can cause leaks. For this reason, seals of this kind are only used for grease lubrication. They serve to prevent dust and other foreign matter from entering the bearing.
Felt seals are not suitable for peripheral speeds in excess of 4 m/s. They should therefore be replaced with synthetic rubber seals as appropriate for the application.